
When the tooling is manufactured and cared for properly, not only can it create good edges, but also keep knives sharper longer. It will either contribute to a good setup or cause a bad one.
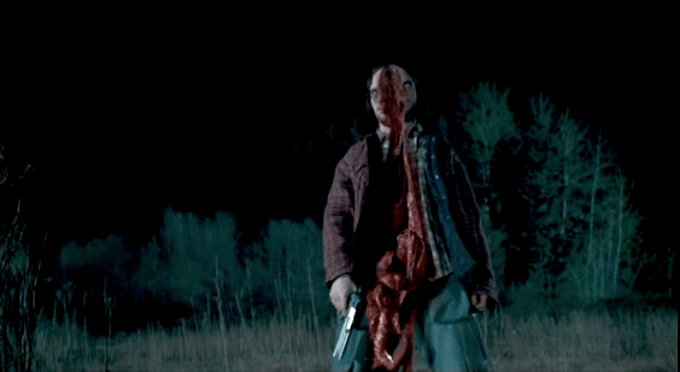
Therefore, it is essential to look at the results, and then adjust as necessary. There are no published formulas or equations that work in every case-or even in most cases. That may sound trite, but slitting-and shearing, for that matter-is a very complicated process. How do you know which clearance is correct? The answer is simple! The one that gives you the best result. Horizontal knife clearance is the most significant coil slitting variable you can adjust to improve slit edge quality. It also can damage tooling, such as the knife and stripper rings, and can even wear out the slitter. Each metal has an optimal clearance, and even the same metal from a different source or thickness might (and usually does) require a different clearance.Įxcessive vertical knife clearance, or overlap, may be the culprit in a multitude of strip defects, including edge wave, crossbow, camber, and deep knife marks. This is true whether you are slitting steel, aluminum, copper, brass, a composite, or any newlyĮngineered metal.
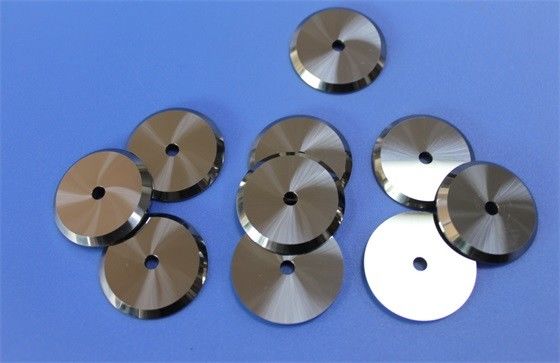
The newer types of slit metals were designed for specific purposes and have vastly different mechanical properties than the older, low-tech metals. Conversely, on thicker metal, the old rules are even less applicable. The thinner the metal, the harder it is to achieve the correct clearance. However, 10 percent is rarely the correct clearance. There are a few metal thicknesses and types on which the 10 percent rule happens to work For example, a 0.008-inch clearance was used to slit 0.080-in.-thick metal. In the "old days," the clearance was almost always set to 10 percent of the metal thickness. Horizontal knife clearance is the most significant of these variables (see Figure 2). Because of advances in equipment, tooling, and software, it is now possible to control the variables and to improve the slitting process to achieve results never before possible. Slitting has been thought of as an art, but it is increasingly becoming recognized as a science. If the line is uneven or the break is rough, it is a bad edge, caused by improperly set cutting knives. If the line is straight between the nick (shiny) of an edge and the break (dull area) and the fracture is clean, it is a good edge. To achieve a good slitting result, each variable that can be controlled must be controlled. Slitting encompasses many variables, and most of them can be controlled. Some slitting problems can be attributed to poor metal quality however, it is much more common for the problems to be caused by other variables and factors during the slitting process. If the line is straight between the nick and the break and the fracture is clean, it is a good edge (see Figure 1). Normally there is a nick (shiny) and a break (dull) area on the edge. Look at the edge! On most common slit thicknesses, a 30x microscope is ideal for this purpose. How can you recognize a good edge? It's not as hard as it sounds. When slitting problems arise, the edge is the first place to inspect. These include poor edge quality, edge burr, edge wave, camber, crossbow, knife marks, and slit width that is out of specification. Many problems can arise during metal slitting. Good coil slitting tooling and practices result in good edge quality.
